Listening and responding to our customer’s wants and needs has created an Industrial Refrigeration manufacturing process like none other. Our process does not start at the entry to our building but rather at our customer’s facility. Integrating new technologies to best serve the customer has redefined our perspective and led us to focus on what is truly important to the success of our installation.
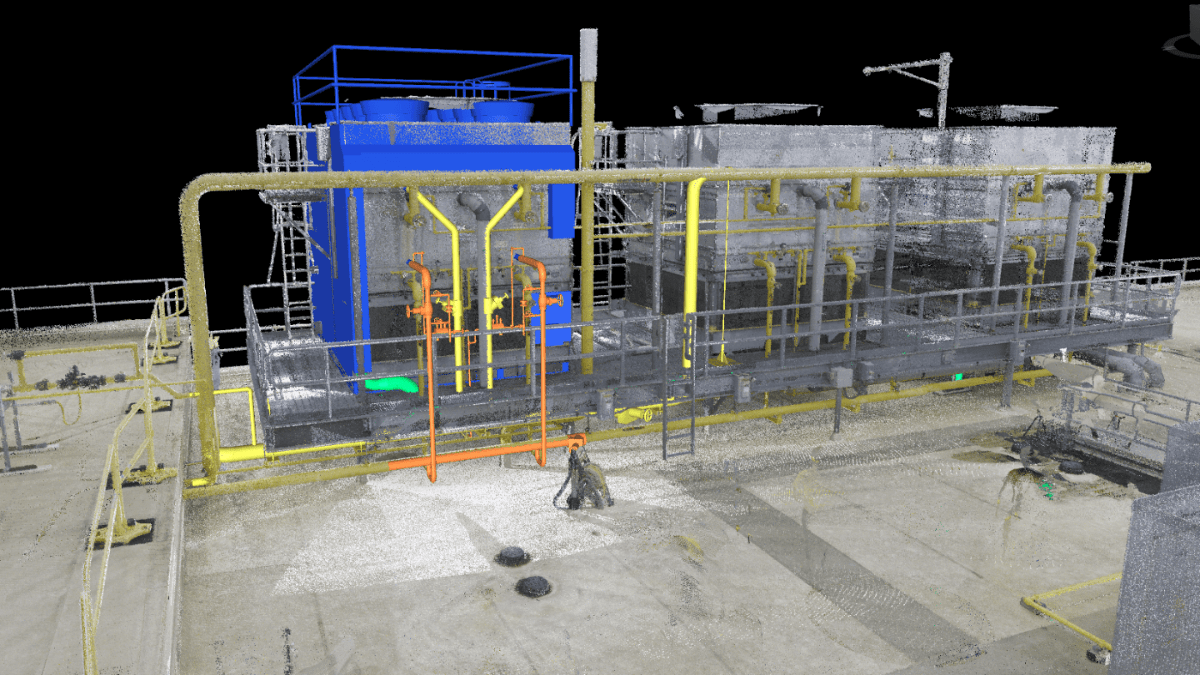
We are often challenged with complex solutions to unique problems. Consider an example of a crowded engine room in need of the addition of several additional compressors, a new condenser to be installed overhead, as well as the addition of the required piping, valves, pumps, fittings, and vessels. What would make this system expansion ideal for the customer?
3D MAPPING
Customers need quality solutions – fast. In a few short hours, we can create an exact three-dimensional map of the engine room. It will include everything needed to enable an accurate and timely assessment. With advanced technology and trained experts, we assemble millions of points of data to develop a precise, to scale, 360° map of the room, and everything in it.
EXPERT PLANNING
With this information, we can collaborate to develop an engineered installation solution on top of this 3D map, ensuring that the piping and all the additions considered are routed to avoid structure, existing piping, conduit, and other potential obstructions. Applying attention to detail, all code and regulatory requirements are integrated into this solution as well.
ROBOTIC PRECISION
The final approved design can be broken down into pipe section drawings and “cut” files from these drawings can be exported electronically to our five-axis, computer-controlled (CNC) pipe cutting machine. With the CNC process, we can make all the pipe cuts, bevels, and scribes required for factory assembly of large sections of piping runs. All of this metal pre-fabrication work, due to this advanced machine technology, would be prepared with unparalleled robotic precision.
PREFABRICATED SOLUTIONS
As our customers run busy food production or storage facilities, it is preferred that over 80% of the welds would take place at our manufacturing facility. For our customers, this reduces the hot work/fire watches required at their site, enhances safety, and reduces the on-site debris associated with the construction process.
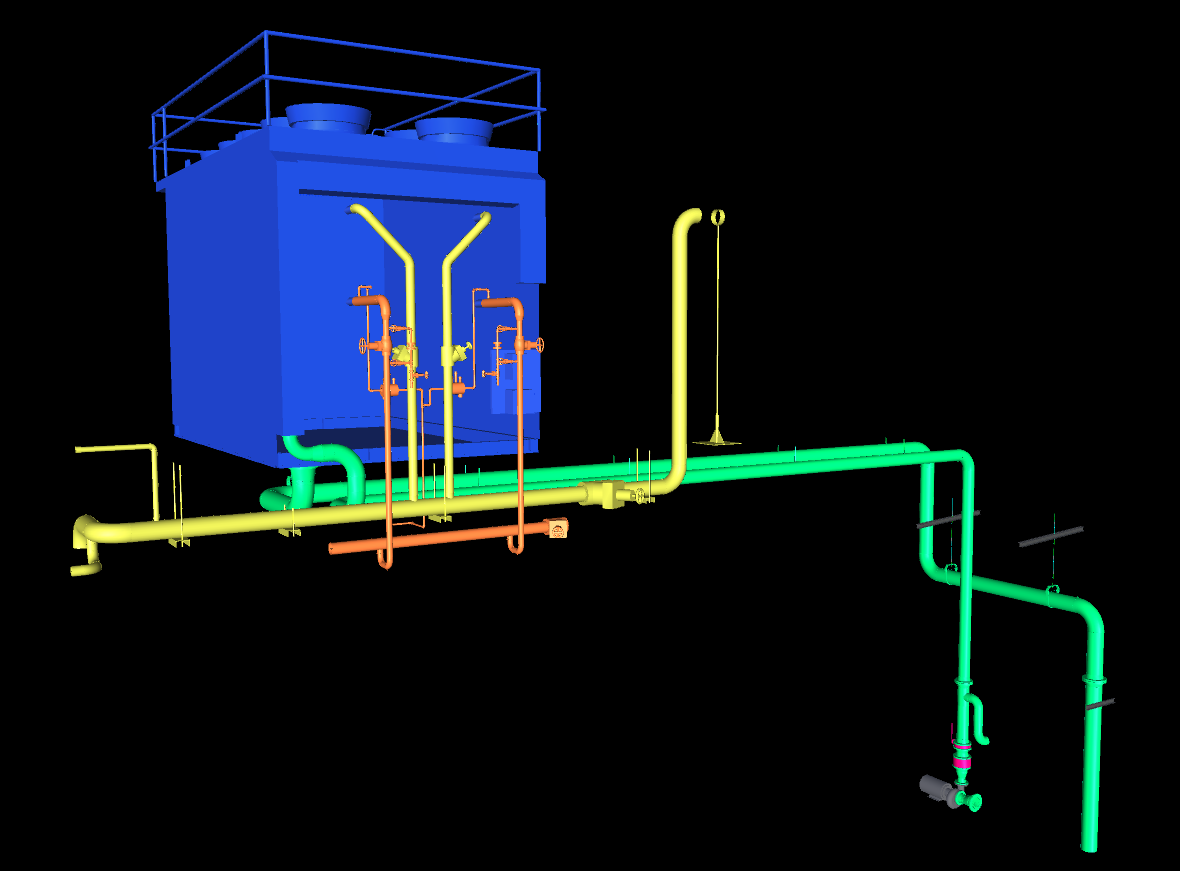
Prefabrication does not require that boxes of valves and fittings be sorted through and assembled at the customer’s locale, speeding the work to be done and minimizing site disruption. Our crew can be at the customer’s facility for a minimum amount of time, assembling pre-fabricated pipe runs, supports, skid packages, and vessels that fit perfectly and arrived where they were needed when the field crew needed them.
This type of complete, efficient response has been developed based on our customer’s needs and reflects the most advanced thinking in our industry. We offer state-of-the-art virtual design and construction technology. We employ scanning technology, robotic total stations, and we have conducted extensive training. We’ve developed and assembled a broad array of 3-D models of pipe, valves, fittings, and refrigeration equipment in our database. We’ve constructed the processes and have an extensively trained team of experts, enabling the electronic transition from laser-generated models to computer-controlled fabrications on our manufacturing floor.
We have a knowledgeable team of refrigeration engineers and PSM professionals ensuring that all regulatory requirements for natural refrigeration systems are adhered to. Beyond that, we’ve spent nearly fifteen years embedding LEAN processes into our practices and culture, ensuring that the output from our manufacturing facility arrives on time, every time.
This is a very unique, customer-oriented, customized, project-based approach to operations, and we are proud to employ these industry-leading methods to serve our customers.
Access our Qualifications Booklet for more details on what to look for when choosing a qualified contractor.